Flotation Height in 'Air Hockey' Spatial Atomic Layer Deposition
Atomic layer deposition(ALD) is one proven method to deposit ultra-thin films. ALD is advantageous for its atomic-level thickness control and conformity; leading to high quality films. Slow deposition rates for conventional ALD contribute to the impracticality of utilization of this technique for high throughput processing. Spatial ALD operates by continuously supplying the precursors while keeping them physically separated in different zones; eliminating the essential time intensive purging step in conventional ALD. The deposition rate is drastically improved in spatial ALD due to the enhancement of the mass transfer of precursors to the substrate, transforming the process to being kinetically limited. The magnitude of this effect may be correlated with the distance separating the precursor inlets and the substrate. Advances in the deposition rate improvement requires an extensive understanding of the fluid dynamics of the gases and its dependence of the process parameters. A novel spatial ALD system that operates analogously to an air hockey table is being developed with the aid of COMSOL Multiphysics. The fluid mechanics of the system are not well understood and COMSOL is used to gain insight to the underlying physics. It is believed that the flotation height of the substrate may be the most significant factor in determining the quality of film deposited. The height of the substrate is determined from its vertical force balance; the magnitude of the upward force caused by the pressure of the fluid must overcome the downward force of gravity on the substrate. COMSOL is used to evaluate the pressure distribution under the substrate, accounting for both the inlet and exhaust vents. A moving mesh is incorporated in a study involving the fluid-structure interaction multiphysics interface to solve for the pressure distribution. Livelink with Matlab extracts the pressure distribution and integrates it to calculate the upward force. The upward force is uniformly applied to the substrate to determine the gap height, based on the inlet conditions. Developing a relationship between the inlet conditions and the gap height is significant for allowing for thorough control of the parameters during experimentation leading to a more complete characterization of films. Additional calculations are made to determine the pressure at the exhaust vents which are coupled with the gap height. Future computational studies will focus on the effectiveness of the diffusional nitrogen barrier. A complete understanding through computational efforts in COMSOL contributes to improved design and development of future systems.
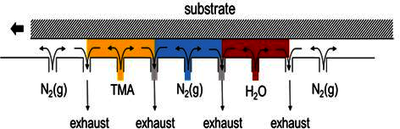
ダウンロード
- grasso_poster.pdf - 0.65MB
- grasso_abstract.pdf - 0.04MB