CFD Simulation of Micro-channel Heat Sink used for Cooling Applications
Microfluidic device based applications are gaining importance since the last few years, mainly because of its potential of replacing large-sized equipment with relatively compact devices. Micro-channel heat sinks are one of the widely investigated applications as they can provide a very effective and innovative cooling technology to remove a large amount of heat per unit area. It is therefore important to understand the fluid flow and heat transfer behavior in such systems. In earlier studies, experimental investigations related to such systems have been carried out and numerical models have been proposed and solved by conventional methods [1]. CFD (Computational Fluid Dynamics) has become a very useful tool in recent years to study such complex systems and plays an important role in deciding the best operating parameters. In this work, a CFD study of flow and heat transfer through a micro-channel heat sink system was carried out by developing 3-D transient models with an objective to obtain more effective model and predict optimum performance parameters which can be used for further analysis and exploring possibilities to modify designs. The design and initial operating parameters for the system under consideration were taken from the literature [1]. Navier-stokes and energy balance equations were representing momentum and heat transport respectively through the sink. A CFD software COMSOL Multiphysics® was used for modeling and simulation purposes. Laminar flow, Heat transfer in Solids and Heat Transfer in Fluids modules existing in COMSOL Multiphysics®
were chosen to represent the developed model. The model predictions include pressure drop, heat loss (transfer), velocity distribution and temperature variation in the sink for various ranges of input parameters. The results related to the profiles are found to be in good agreement with the corresponding experimental data. The effect of the inlet flow rate of water (or Reynolds number (Re)) on pressure drop was then studied and the results were compared with those obtained experimentally. It was found that the percentage of error is minimum (1.701%) for Re = 808 and maximum (14.16%) for Re =1960. The error percentage varies in a very irregular fashion from Re = 500 to 1960, but the error is relatively more for Re > 1400. Hence the developed CFD model is found to be effective for low flowrates and needs to be modified further to make it suitable for higher desired values of flowrates. It was found that the amount of heat loss is maximum at the inlet and the temperature of the coolant (water in this case) is increasing along the length of the sink. Heat loss through water (single slot) is expected around 200 J. Thus the results of simulations are in appreciable agreement with the experimental results under specified constraints and limitation and thus can be employed for a new design.
- W. Qu, I. Mudawar, Experimental and numerical study of pressure drop and heat transfer in a single-phase microchannel heat sink, Int. J. Heat and Mass Transfer, 45, 2002, 2549-2565.
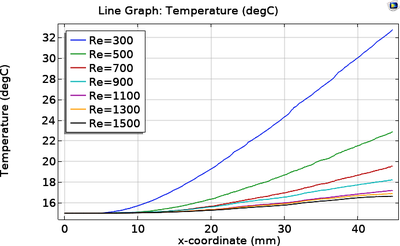