Development of improved ultrasonic transducers for medical surgery
Finite element modelling of surgical transducers has been performed and is described.
Ultrasonic transducers vibrating at around 25 kHz are used in orthopaedic surgery to cut bone. The high acoustic impedance of the metal blades used in these devices couples energy more efficiently to materials with high acoustic impedances, such as bone, whereas materials with low acoustic impedances, such as soft-tissue, are coupled weakly. Apparently, this results in preferential cutting of bone rather than soft-tissue, which can be advantageous during surgery.
The Langévin type of transducer is a common design of power transducer used in many applications, including applications in orthopaedic surgery. A Langévin transducer is essentially a solid rod that vibrates as a half-wave, longitudinal resonator with a nodal point at its centre and anti-nodes at both ends. Some designs of Langévin transducer for surgery incorporate the blade into the half-wave, longitudinal resonator, resulting in the tip of the blade being an anti-node with a large displacement. Other variants of the Langévin transducer for orthopaedic surgery have longer blade assemblies, often including horns to amplify the displacement.
It is possible to make one finite element model of the main driving Langévin unit and a second model of the extended blade unit, including any amplifying horns. The two models of the transducer can each have their dimensions adjusted so that they have the same half-wave longitudinal resonating frequency before physical units are built and tested. This modular development approach has been the way that conventional ultrasonic design has progressed in the past and is still preferred if the final assembly is physically modular, say with interchangeable blade units. Alternatively, the two parts assembled as one entity can be one finite element model; in this alternative approach the desired mode of longitudinal vibration is a full-wave resonator with anti-nodes at each end and two nodes at separate points along the length.
Results of finite element models are compared for the two different approaches for developing new medical transducers: single entity or two units tuned to the same frequency. The effect of varying material properties is considered and so too is the effect of loading of the cutting edge, which can result in a change of vibration mode from longitudinal to flexural. A change in mode of vibration can result in a loss of cutting efficiency and increased generation of heat that can cause burning of the bone.
Finite element models have been developed in COMSOL Multiphysics® using the piezoelectric devices interface, which incorporates both structural mechanics physics and piezoelectric physics. Solutions have been obtained using the eigenfrequency solver: to find resonant frequencies of different modes with animation used to identify the longitudinal half-wave or full-wave modes of vibration.
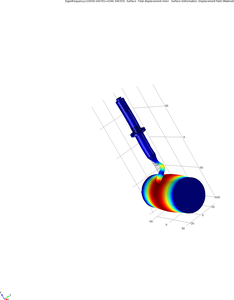