Numerical Prediction of Weld Bead Geometry in Plasma Arc Welding of Titanium Sheets
Plasma Arc Welding (PAW) is one of the important arc welding processes commonly used in electronics, medical, automotive and aerospace industries due its high accuracy, finishing, and ability of welding any hard materials. It is an extension of Tungsten Inert Gas welding (TIG or GTAW). PAW has been unnoticed because it is more complex and requires more expensive equipment compared to other commercial arc welding processes. On the other hand, the automotive manufacturers lean to plasma arc welding for a number of applications, such as exhaust system components and body panels. The joining of titanium sheets is highly difficult and extra attention is required to ensure adequate shielding is to be provided in a proper way because these materials are less tolerant of contamination. Titanium has a strong chemical affinity for oxygen, a surface oxide layer is developed on the substrate metal and the metal becomes highly susceptible to embrittlement by nitrogen, hydrogen and oxygen. Therefore, the welding of titanium sheets is still an emerging technology in industrial sectors.
The present investigation deals with the numerical simulation of plasma arc welding of 2 mm thick Ti-6Al-4V alloy using finite element method of COMSOL Multiphysics® software. A Modified Three Dimension Conical (MTDC) heat source model is considered for predicting the temperature distribution on thin sheets of titanium alloy. The temperature dependent material properties of Ti-6Al-4V such as thermal conductivity, specific heat and density are used for performing the simulation. In the developed FE model, all the physical phenomena such as losses due to conduction, convection and radiation are taken into account. The result of the numerical analysis provides the shape and size of the weld bead from the simulated temperature distribution plots, which is then compared with the results obtained from experimentation. It is observed from the results that the predicted weld bead geometry with corresponding experimental results and are found to be in good agreement.
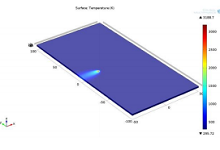
ダウンロード
- dhinakaran_presentation.pdf - 1.51MB
- dhinakaran_poster.pdf - 0.62MB
- dhinakaran_paper.pdf - 0.68MB
- dhinakaran_abstract.pdf - 0.02MB