資料
ホワイトペーパーとアプリケーションノート
Simulation of an Electromagnetic Sheet Shearing System
Published in 2015
Electromagnetic shearing (EMS) is a high speed sheet metal shearing system where the workpiece is fractured under a pulsed electromagnetic force. It can be regarded as an extension of electromagnetic forming[1-2]. The basic shearing principle is that a huge repulsive electromagnetic force is generated in the driver plate under the action of pulsed magnetic field and induced eddy current, and then the driver plate can be actuated for pushing blade quickly towards the steel sheet. Therefore, the driver plate and pulsed magnetic field generation equipment are the basis of the electromagnetic shearing system.
To study the feasibility of electromagnetic shearing for medium plate, this paper presents the use of COMSOL Multiphysics® to analysis the motion behavior of the plate driven by a pulsed magnetic field. We build a simplified 2D axis-symmetric model including a plate and a coil. There are four models used in the simulation: 1) “Global ODEs and DAEs” model; 2) “Magnetic Fields” model; 3) “Solid Mechanics” model; 4) “Moving mesh” model, which are solved using a time-dependent fully coupled solver. The first three models are used for circuit analysis, electromagnetic analysis and mechanical analysis, respectively. The partial differential equation (PDE) used in the first model is derived from the equivalent RLC circuit of the EMS system (see Figure 1). The last model is taken to update the shapes of the mesh elements with the motion of the plate. With the proposed finite element method, the magnetic force distribution in the driver plate and motion behavior of the plate is analyzed. Numerical results from COMSOL Multiphysics® were validated with the theory of the electromagnetic shearing developed earlier.
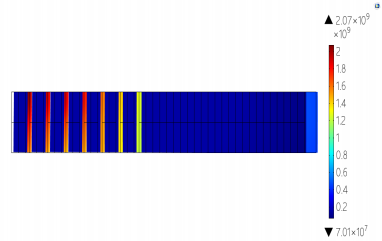
ダウンロード
- 黄_poster.pdf - 0.69MB
- 黄_abstract.pdf - 0.04MB