Thermo-Electrical Improvement of a MEMS-IR-Emitter Membrane
NDIR (Non-dispersive infrared) sensors are state of the art for measuring gas concentrations in the Mid-infrared spectrum, e.g. components of exhaled human breath. These sensors require fitting light sources. Micro light bulbs and other filament based light source are sensible to mechanical shock and require mechanical choppers for high modulation frequencies. MID-IR-LEDs are only available up until 4 µm and quite expensive so far. However, the so-called fingerprint region, where organic compounds have their characteristic vibration spectra just starts above 6 µm. To analyze substances at these higher wavelengths MEMS-IR-emitters are the only suitable source for lightweight and cost-efficient measuring systems. When designing a MEMS-IR-emitter, which is basically a radiative ohmic resistance embedded within a very thin (~ 1 µm) membrane structure, there are many challenges regarding manufacturing, operating lifetime, spectra, response time, radiative intensity. Furthermore, some of the required properties are contradicting – e.g. the bigger the emitter surface, the bigger its radiant intensity, however the slower its response time. A smaller emitter is faster but has less emission intensity. Moreover, the emitter’s current density is proportional to its radiant intensity but inversely proportional to its lifetime – that is dominated by electro migration effects. Time dependent measurements require a pulsed sensor operation. Usually, industrial users expect measurement frequencies of minimum 20 Hz – some applications (e.g. breath analysis) demands sample rates of at least 100 Hz. Current commercially available MEMS-IR-emitters already reach their usability limit at 10 to 20 Hz. The investigated MEMS-IR-emitter contains an already thermo-mechanical optimized multi-layer system of several dielectric layers and one conductive layer. It is possible to customize the geometrical design of the conductive layer and add an outer layer of silicon for heat dissipation. After establishing a verified simulation model of our state-of-the-art MEMS-IR-emitter version, the target of the here presented study is, to achieve higher pulsing frequencies with sufficient radiant intensity and device lifetime. Therefore, different geometries of the conductive layer (full surface, meander, neckings) and different additional structures with variated geometries for better heat dissipation are studied within this work.
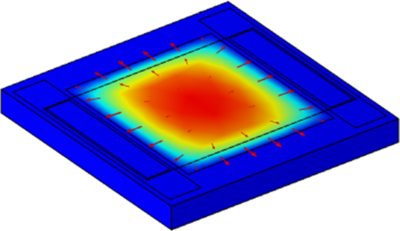
ダウンロード
- Poster_v2.pdf - 1.55MB