When Precise Numerical Predictions Come to the Rescue of Liquid Lubrication
Whereas some bearings designed in the 19th century are still working properly nowadays, some others which were recently designed encountered premature failures. Tribological applications, such as journal bearings or rolling element bearings, are generally ruled by complicated multiphysical phenomena. Consequently, the predictions on the lifespan or the efficiency of these applications are sometimes not reliable and occasionally totally wrong. An appropriate numerical model is one of the most efficient mean to better understand the physics of these applications. This is particularly true when it is combined with other approaches such as experimental measurements. An appropriate model involves the solving of the Reynolds equation with a relevant modelling of the cavitation. The lubricant may also show piezo-viscous and non-Newtonian response which should be included in the constitutive relations. When high hydrodynamic pressure is encountered, solid deformations may also play a role. The contact would then follow an elastohydrodynamic behaviour. Moreover, the lubricant shearing is very likely to generate a significant heat. This implies that the temperature distribution should also be computed in the solids and the fluid to predict the actual system behaviour. A simple tribological application, the lubricated pad, is presented in this article. The potential impact of the different physical phenomena is evaluated thanks to a numerical model built with COMSOL Multiphysics®. Providing a precise and quantitative prediction on film thickness, friction, lifespan or efficiency is beyond the scope of this article. However, its goal is to address the different challenges that may be involved under different working conditions. A COMSOL application based on the model developed for this tribology case is also developed. It can be used with COMSOL Server™.
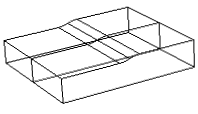
ダウンロード
- wheeler_presentation.pdf - 1.78MB
- wheeler_poster.pdf - 0.58MB
- wheeler_paper.pdf - 0.92MB
- wheeler_abstract.pdf - 0.02MB