Fluid–Structure Interaction in Aluminum Extrusion
Application ID: 4386
In massive forming processes like rolling or extrusion, metal alloys are deformed in a hot solid state with material flowing under ideally plastic conditions. Such processes can be simulated effectively using computational fluid dynamics, where the material is considered as a fluid with a very high viscosity that depends on velocity and temperature. Internal friction of the moving material acts as a heat source, so that the heat transfer equations are fully coupled with those ruling the fluid dynamics part. This approach is especially advantageous when large deformations are involved.
This model is adapted from a benchmark study. The original benchmark solves a thermal-structural coupling. The alternative scheme modeled here couples non-Newtonian flow with the heat transfer equations. In addition, because it is useful to know the stress in the die due to fluid pressure and thermal loads, the model adds a structural mechanics analysis to the other two.
A comparison between the available experimental data and the numerical results of the simulation shows good agreement. On the basis of the results from the simulation, the engineer can improve the preliminary die design by adjusting relevant physical parameters and operating conditions.
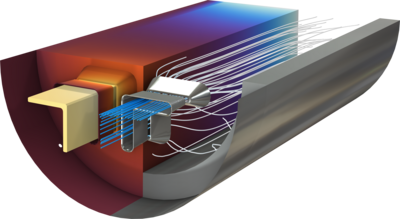
この model の例は, 通常次の製品を使用して構築されるこのタイプのアプリケーションを示しています.
ただし, これを完全に定義およびモデル化するには, 追加の製品が必要になる場合があります. さらに, この例は, 次の製品の組み合わせのコンポーネントを使用して定義およびモデル化することもできます.
- COMSOL Multiphysics® and
- either the MEMS モジュール, or 構造力学モジュール
アプリケーションのモデリングに必要な COMSOL® 製品の組み合わせは, 境界条件, 材料特性, フィジックスインターフェース, パーツライブラリなど, いくつかの要因によって異なります. 特定の機能が複数の製品に共通している場合もあります. お客様のモデリングニーズに適した製品の組み合わせを決定するために, 製品仕様一覧 を確認し, 無償のトライアルライセンスをご利用ください. COMSOL セールスおよびサポートチームでは, この件に関するご質問にお答えしています.