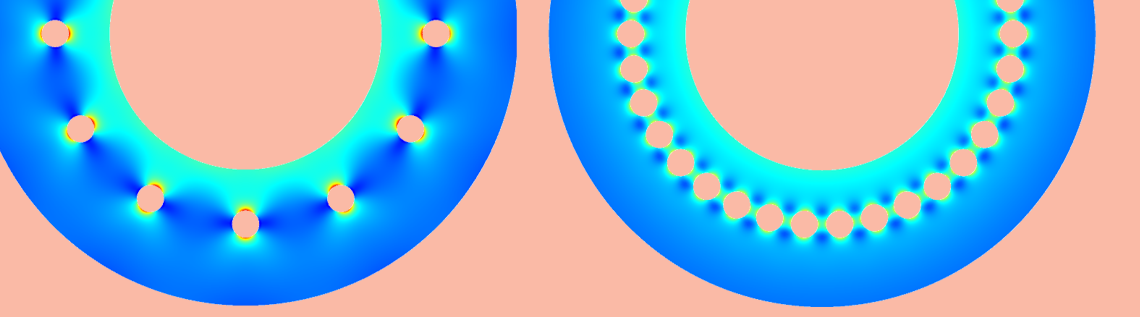
構造物の応力が許容限界を超える場合, 最初に頭に浮かぶのは, 材料を追加して耐荷力を高めることです. これは多くの場合良い選択ですが, 反対の方法をたどる必要がある場合もいくつかあります. 材料を除去して構造を改善することです. このブログでは, そのような例をいくつか調べます.
追加された穴の謎
約30年前, ある種の遠心分離機の応力を解析しました. 問題は, いくつかの穴 (分離されている物質の1つが排出される穴) の周りの応力が高すぎることでした. さらに穴を追加するだけで問題を解決できる (実際にはスループットも向上する) とお客様に提案したところ, 十分に納得していないようでした. ただし, いくつかの有限要素解析がそのポイントを証明しました. 原則として, 構造は次のようになりました.
フォン・ミーゼス応力分布とともに, 遠心分離機の一部の概念図. 荷重は遠心力によって引き起こされます.
プロットに主応力矢印を追加することにより, 実際に何が起こっているのかをよりよく理解することができます:
円周に12個の穴がある, 元のジオメトリの最大主応力のプロット.
主な応力成分は円周方向に作用しており, 応力集中は応力流の方向転換によって引き起こされます. 実際, 穴を円周方向のスリットに置き換えることができれば, 応力集中はまったくありません. ただし, リングの内側と外側を接続する必要があるため, これは不可能です. 穴を互いに近づけると, 応力流束の方向転換が少なくなります. 最適化手順を使用して穴の最適な分布を見つけることができますが, この場合, パラメーターを手動で変更するだけで簡単です. 34個が適切な数であることがわかります.
34個の穴があるため, フォン・ミーゼス等価応力が33%減少します. 同時に, より軽量な構造とより優れたスループットが得られます.
12穴と34穴の遠心分離機におけるフォン・ミーゼス応力の比較.
主応力の拡大図を見ると, 穴をさらに近づけることができない理由がわかります. それらの間の間膜は, 遠心力によって半径方向の応力を受けるため, 薄くすることはできません.
34個の穴を使用した場合の最大主応力.
フィレット
形状に急激な変化がある場合, 応力集中が発生します. 経験豊富な設計者は, 繊維部分をできるだけ滑らかにし, 大きなフィレット半径を使用しようとします. ただし, フィレット半径を大きくすると, 追加された材料が他のパーツと干渉する可能性があるため, 実行できない場合があります.
この場合, アンダーカットまたはレリーフ溝と呼ばれるデザインを使用できます. この場合, 材料を削除して半径を大きくします. (溶接の文脈では, アンダーカットは通常, 特定のタイプの溶接欠陥を意味することに注意してください)
以下の例では, 3つの異なるデザインを見ることができます. 元の設計 (上) では, 応力集中係数は1.91です. フィレット半径を50%増やすことにより, 応力集中係数を13%減らして1.67にすることができます. 赤い破線は, 薄い部分の厚さが一定であるところを示しているため, フィレット半径を大きくすると, スペースが失われます.
3番目のケースでは, 代わりに, より大きな半径のアンダーカットが使用されています. これにより, 応力集中が同じように減少しますが, 厚みのある領域が拡張されるという欠点はありません. アンダーカットを使用することの欠点は, 部品の製造がより複雑になり, したがって費用がかかる可能性があることです.
2つの異なる幾何学的変化を使用した応力集中の低減.
リリーフ溝が非常に効率的である特殊なケースは溶接です. 溶接自体は通常, 疲労に非常に敏感であるため, 溶接の前に溝を追加することで溶接をシールドできる場合があります. 実際には, 疲労強度の違いにより, 溶接止端の場合よりも溝にかなり高い応力を許容できる場合があります.
変位制御
構造物への荷重が, 規定の力ではなく制御された変位で構成されている場合, 材料を追加すると, 通常, 力が増加します. 応力は一定であるか, さらには増加します. 一見, 変位が制御されているように見えない場合が多くありますが, それでも制御されています. 熱変形は, 多くの場合, 既定の変位の一種と見なすことができます.
次の2D の例を考えてみましょう:
ジオメトリと境界条件.
3本の棒は右側で0.1 mm の既定の変位で引き伸ばされます. モデルの左側では, 対称面が想定されています. 結果として生じる応力分布を以下に示します.
既定変位下での応力分布 (変形は100倍に拡大されます).
穴の最大応力は 188 MPa です. 2つの外側のバーの力は 3.36 kN ですが, 中央のバーの力は 3.22 kN です. これで, 剛性を下げることにより, 重要な中央バーの力と応力を下げることができます. もちろん, これはさまざまな幾何学的変化によって実現できます. 実際には, オプションは通常, 構造の機能によって制限されます. ここでは, 対称面に大きな半径のノッチを作成します.
変更の効果は, 最大応力が 19% 減少して 153 MPa になることです. より多くの材料を除去することにより, さらに大きな削減を達成するのは容易であることは明らかです.
他の2つのバーで何が起こったのでしょうか?既定変位のため, 以前よりも伸びるはずはありません. 力を解析すると, 実際には 3.36 kN に増加したことがわかります. つまり, 1% 未満です. わずかに増加する理由は, 規定変位がバーに直接適用されるのではなく, 弾性がありますがかなり剛性のある構造を介して適用されるためです. これは通常, 実際の構造に当てはまります.
荷重パスの変更
前の例と同じジオメトリを考えてみましょう. 既定変位の代わりに, 力が荷重として使用されます. 値は, 規定変位によって引き起こされた反力と正確に一致するように選択されます. つまり, 9.94 kN です. 明らかに, 元のジオメトリでは, 結果は同じままです.
ただし, この場合, 中央のバーの剛性を下げると, 2つの外側のバーによってより多くの荷重を運ぶ必要があります. また, 構造物の総剛性が低下するため, 荷重境界での変位は多少増加する必要があります.
力が規定されたときのより柔らかい構造の応力分布.
見てわかるように, ピーク応力の減少は今や小さくなっています. 外側のバーの力は 3.58 kN に増加し, 中央のバーの力は 2.77 kN になりました.
これは, まったく異なるメカニズムの例です. 荷重パスの変更です. 他の部材に力を伝達することにより, 臨界部材の力を低減することが可能です. これを実現する簡単な方法は, 2つの外側のバーを太くすることですが, これは, 材料を削除するのではなく追加することを意味するため, このブログの範囲外です.
構造をより強くするための最終的な考え
材料を取り除くことは, いくつかの状況で局所的な応力レベルを減らすのに有益です. ただし, 上記の例に見られるように, 製造が複雑になることがよくあります.
上記の例では, 変更はエンジニアリングの直感を使用して行われました. パラメーター, 形状, トポロジの最適化などの方法を使用することで, さらに優れた結果を得ることができます. 積層造形法により, 複雑な形状の製造が可能になります.
COMSOL® ソフトウェアで機械的解析を実行するために利用できる機能の詳細をご覧ください.
コメント (0)